Aluminum Extrusions
Aluminum Extrusions
What is aluminum extrusion?
Extruding aluminum is the manufacturing process of creating objects with a specific cross sectional profile by pushing aluminum through a die. This process allows the aluminum extrusion manufacturer to create long lengths of aluminum profiles which can range from very basic tubes or bars to extremely complex designs.
There are three basic categories of shapes that can be extruded. These categories are:
- Solid Aluminum Extrusions: solid rods or other shaped pieces of aluminum.
- Hollow Aluminum Extrusions: lengths of extruded aluminum which contain at least one hollow area inside them such as a square or triangular tube.
- Semi-hollow Aluminum Extrusions: extrusions that are only partially enclosed hollow shapes.
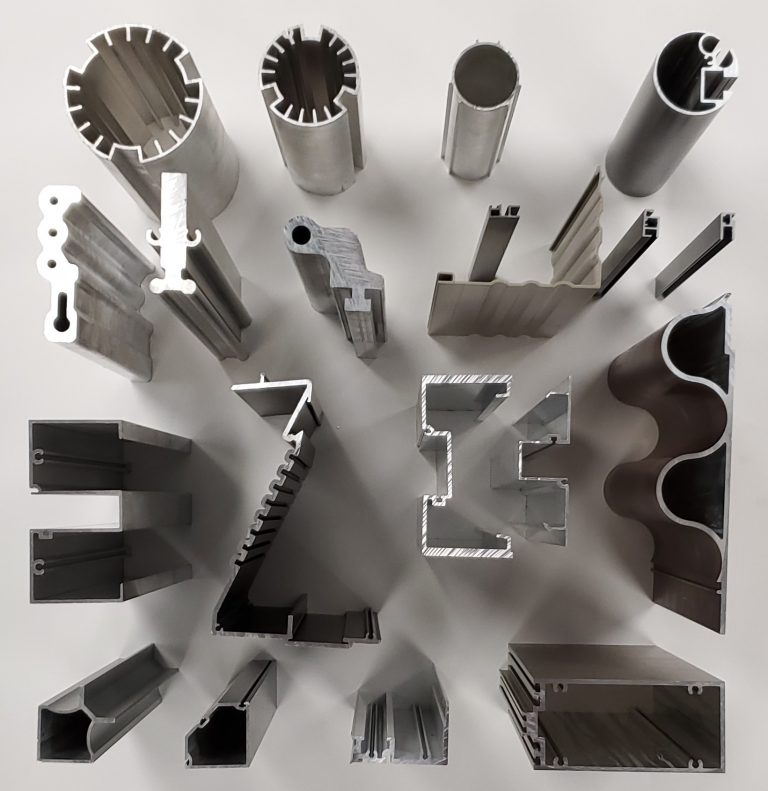
The aluminum extrusion process:
At a very basic level the aluminum extrusion process is the process of pushing aluminum through a die to produce a desired shape from the very basic, to the very intricate, here is the process.
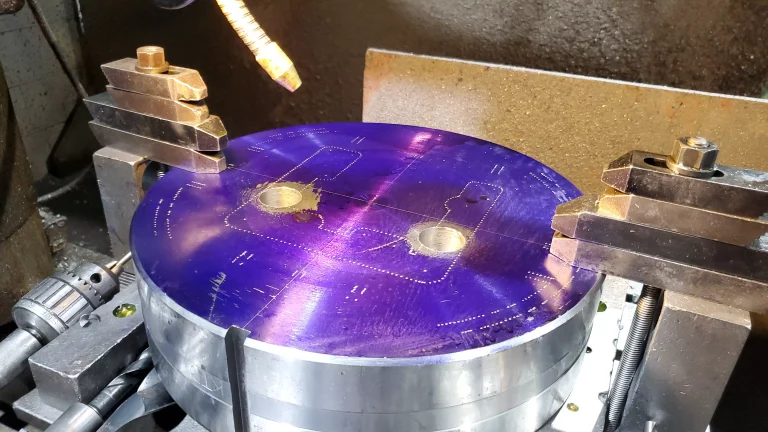
Before aluminum can be extruded a die must be designed and produced to push the aluminum through. This is a service Keymark Corporation provides for our customers. Once a die is available, it is pre-heated then loaded into the extrusion press, this prevents damage to the die, and results in a more even flow as the aluminum travels through the die during the extrusion process.
Once a die has been loaded into the press, aluminum, in the shape of a cylinder, often called an aluminum log, is pre-heated to around 900 degrees. The aluminum is heated to make it malleable enough to push through the die. The aluminum ‘log’ is then cut into a shorter piece of material called a billet which is then loaded into the press. This aluminum billet is then pushed up against the die by a hydraulic ram with extreme pressure forcing the malleable aluminum to flow through the openings in the die and exit the other side in the desired shape.
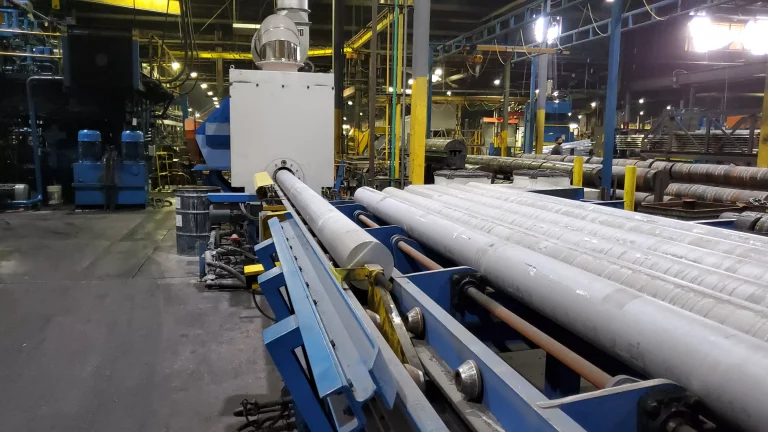
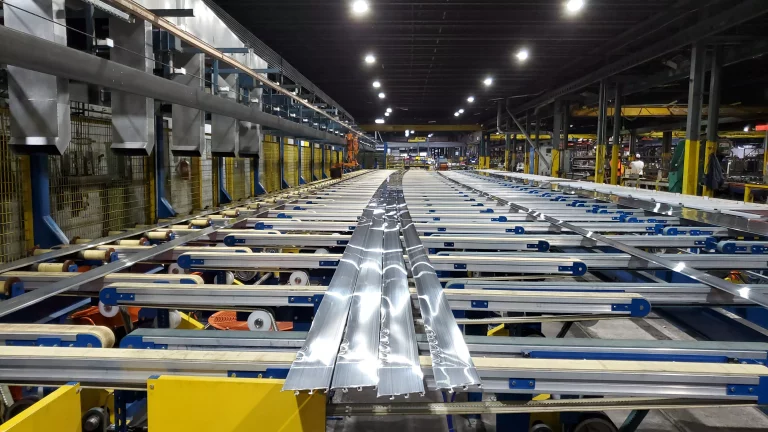
After the aluminum has been extruded, it is transferred to a cooling table where the aluminum extrusions cool down to room temperature. The extrusions can have some twists in them from the extrusion process at this point so they are then transferred to a stretcher. The stretcher pulls the aluminum extrusions from each end of the length until it becomes straight and meets the extrusions expected specifications. At this point, the extrusion is very long so they are cut to a more manageable size then moved on for tempering and finishing before being shipped to the customer.
Quality From The Beginning
Consistent Quality: Our on-site casting facility allows us to control billet cost and quality by producing aluminum logs directly from (P1020) aluminum ingot. Having a cast house on our premises in our Fonda, NY facility, permits us to reuse/recycle internally generated scrap incurred from the aluminum extrusion manufacturing process. Aluminum recycling is an important component in both cost control and environmental sustainability. The process of creating aluminum extrusions begins with the manufacturing of precision-formulated billets in our cast house. Using the most current casting technology, our experienced staff creates billets for most of our extrusion needs. (P1020) Aluminum ingot is purchased from primary producers/suppliers in the United States and abroad and delivered to Keymark on a daily basis.
From casting, the logs go through a process of homogenization that eliminates impurities from the core of the log. Our most recent $ 1.2 million dollar state-of-the-art homogenizing oven at our Fonda, NY facility delivers the highest of quality logs to our extrusion department, ensuring that our customers have a premium quality product built into their aluminum extrusions.
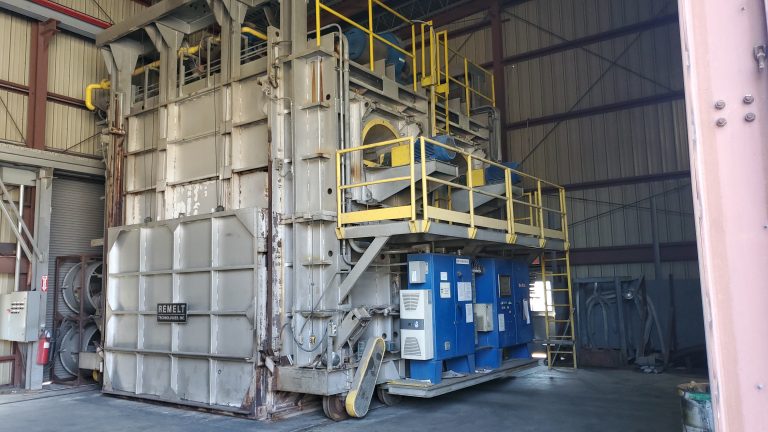
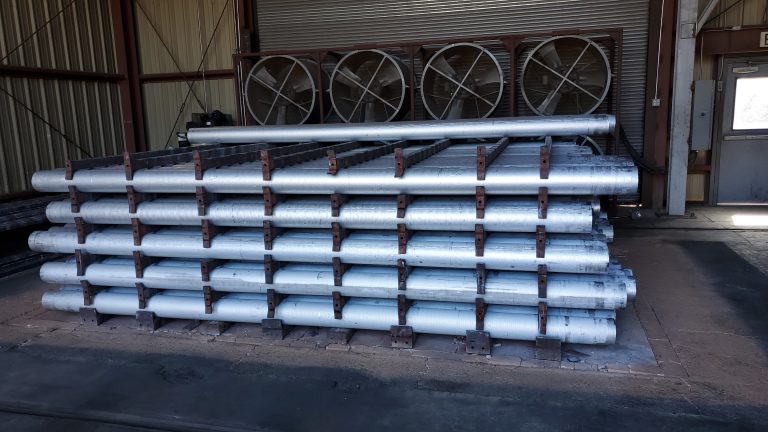
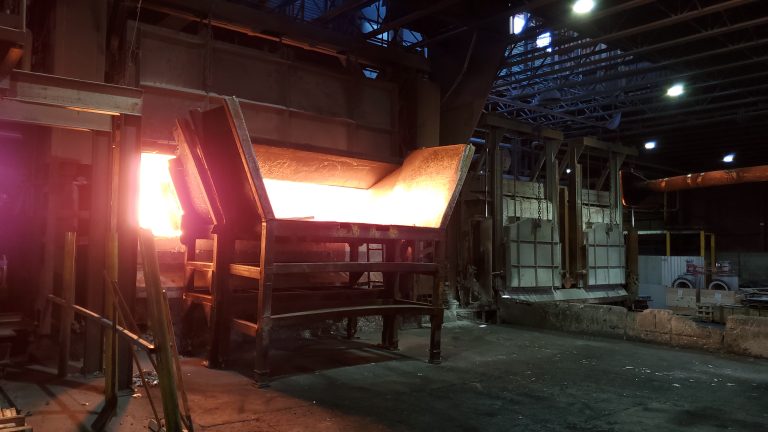
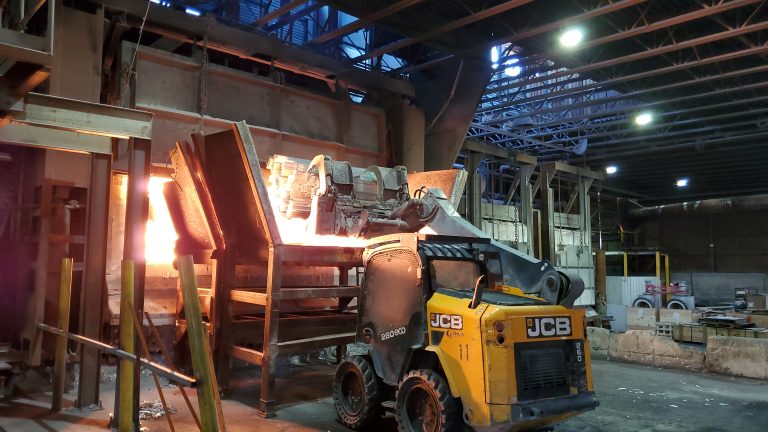
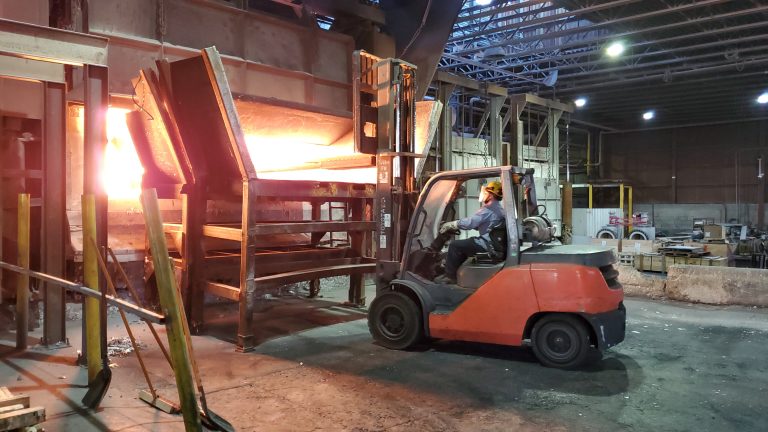
Aluminum Extrusions
Extrusion Capabilities: Since we process only the highest quality extrusion logs in-house, we can ensure continuity of supply and consistent quality for your extrusion needs. Keymark offers prime & recycled billet, either meets or exceeds the specifications required by The Aluminum Association. We use only the finest 6000 series alloys (6063, 6005A, 6061, & 6060) for our extrusion presses. Our extrusion presses incorporate the latest in technology, which allows us to deliver shapes with tolerances that are demanded from the Building and Construction Markets that we serve. We currently operate a wide variety of 8 extrusion presses, which are capable of producing extrusions up to 14″ in circle size.
Keymark also offers a wide array of standard aluminum extrusion dies: aluminum tubing & pipe (rectangular, round & square), rods, bars (square and rectangular), channels, I-beams, and angles as well as other extruded custom profiles for the building and construction industry.
Bring your project to us and allow us to show you what extrusion precision is all about! When you see the Keymark label on your extrusion packages, you know it’s quality.
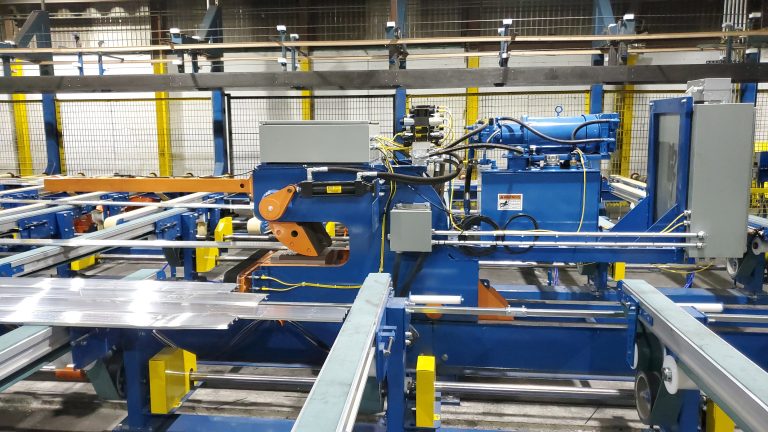
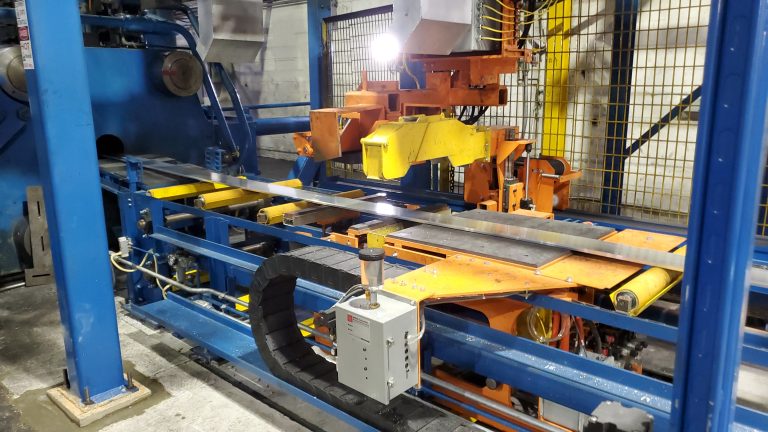
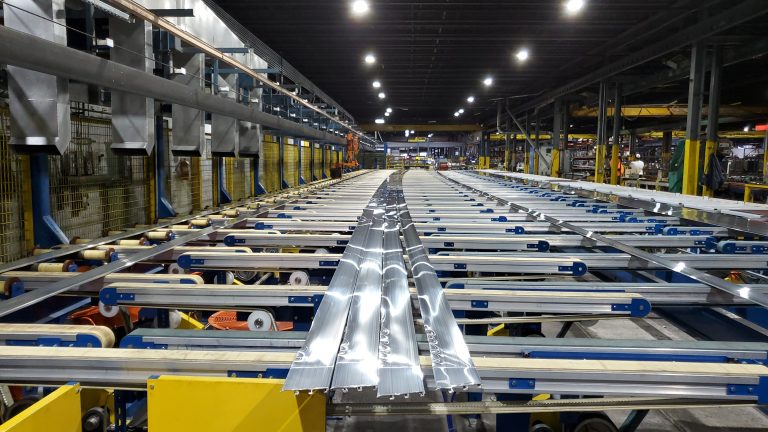