Advantages & Disadvantages of Powder Paints
Advantages & Disadvantages of Powder Paints
Advantages
- Unlike liquid paints, powder coating does not use any solvents…eliminating V.O.C.’s (Volatile Organic Compounds).
- AAMA 2603 powders come with a 10-year factory warranty.
- The mechanical durability of powder greatly exceeds wet paint.
- Requires less energy to produce (Can be up to 30% less than liquid).
- Excess powder in the application process can be reclaimed…eliminating waste.
- Powder can be applied at higher film builds than liquid.
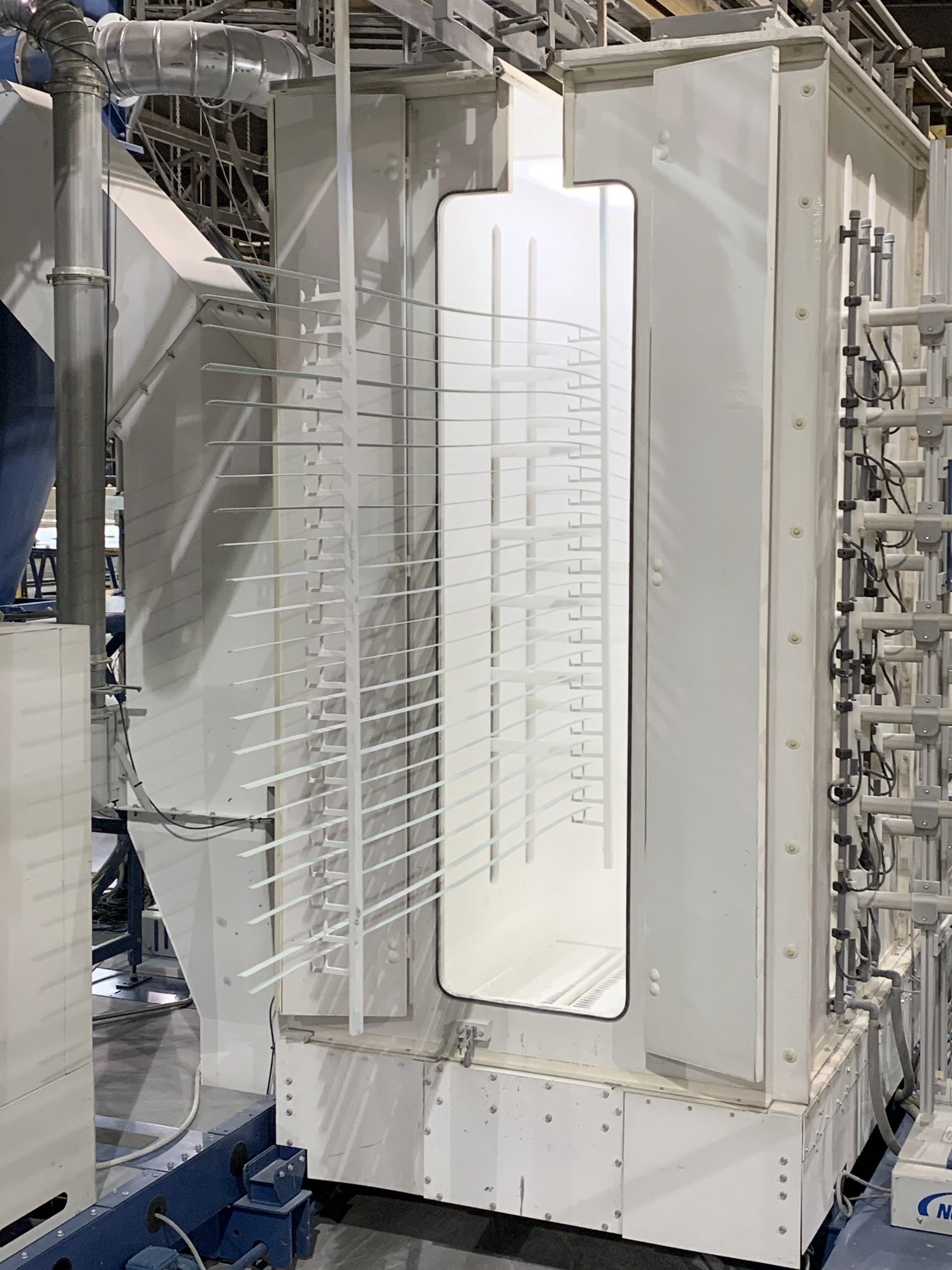
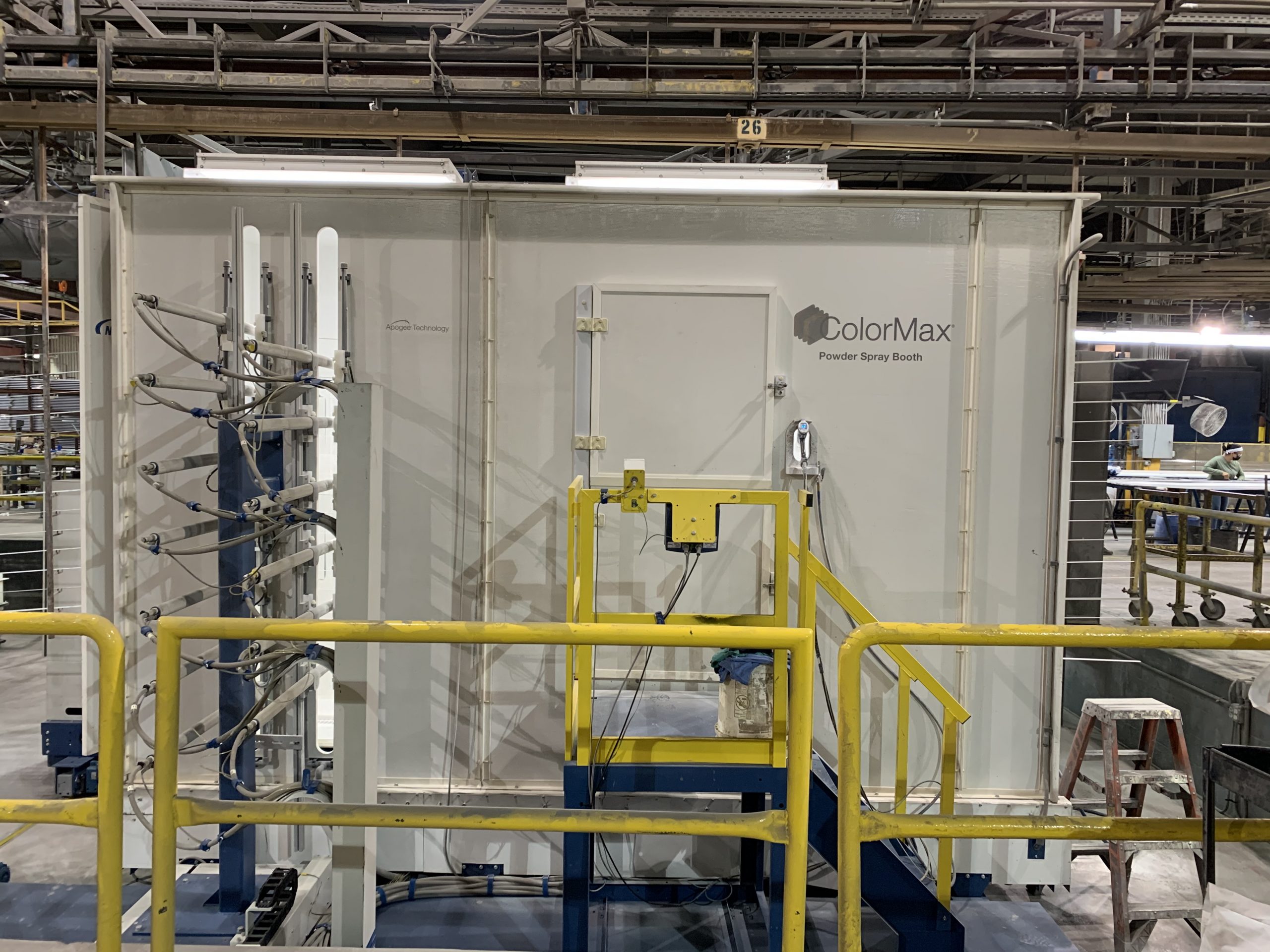
Disadvantages
- Difficult to touch-up in the field with a good color match.
- Applicators cannot perform in-house blending and color matching.
- Powder coating requires a greater film thickness and is difficult to achieve lighter film thickness without creating an orange peel effect.
- Some powder paints are not as economical as their equivalent in wet paints.
- Powder coat paints cannot provide the brilliance of a metallic look as with liquid paints, due to powders inability to hold the same metallic flake content.
- Single coat powder paints on aluminum are susceptible to filiform corrosion.
- Architectural Applications for Liquid and Powder Fluoropolymer Coatings: A Comparative Review
Types of Powder Paints
There are (2) basic types of powder paints:
Thermoplastic – Powders that will remelt when heated
Thermosetting – Powders that will not remelt upon reheating (Keymark sprays only Thermosetting powder paints).
Powder Paint Coating Performance
The Powder Coating Process
- Aluminum Extrusions are loaded on racks and are submerged in a pretreatment tank (40 feet in length) containing chrome phosphate. Chrome Phosphate has proven to be the premier pretreatment for powder paints to ensure the highest level of performance and adhesion. This is also the most important part of the entire painting process.
- Parts are dried in an infrared oven before the application process.
- In the application process, the extrusions travel into the powder booth where powdered resins along with colored pigments are applied to the extrusions through the use of automatic spray guns and an electro-static charge.
- The extrusions then enter a separate high temperature bake oven (350-425 degrees) for approximately 20 minutes and this causes the powder to melt, flow, and then cure, forming a molecular fusion bond.
- The end result is hard surface to coating bonding unlike any other.