Advantages & Disadvantages of Anodizing
Advantages & Disadvantages of Anodizing
Advantages
- Anodizing is durable and will not flake, chip, or peel over time.
- Anodizing is easy to maintain. You only need to do periodic cleaning of anodized aluminum extrusions with a mild detergent and water to restore the original luster.
- Ease of fabrication. The marring usually incurred in fabrication of painted extrusions is virtually non-existent with an anodized extrusion. Other abrasive wear at installation, shipment, and handling is negligible.
- Color sustainability, because of the sealing process during anodizing, helps to keep your extrusions looking factory new for years to come.
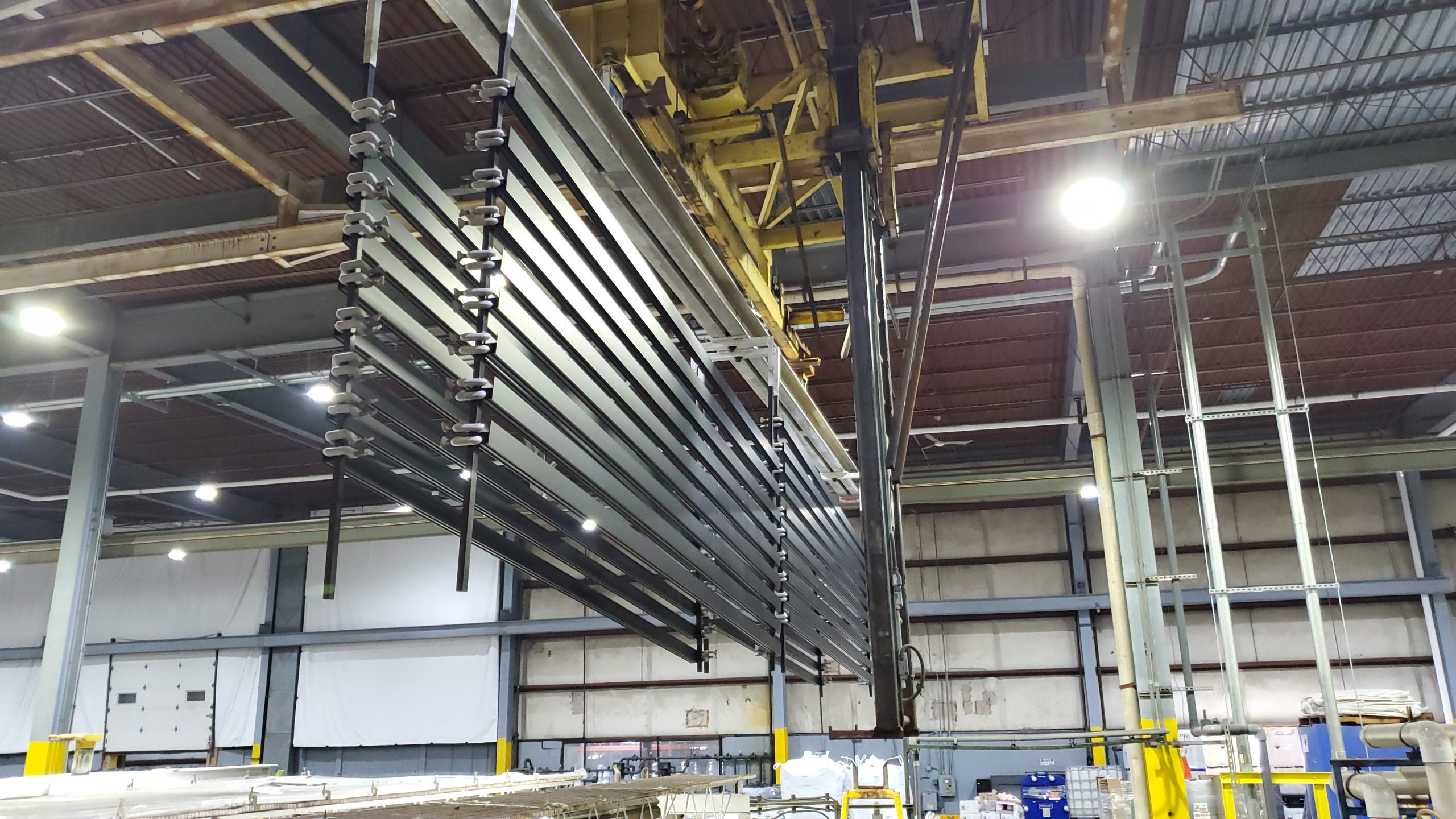
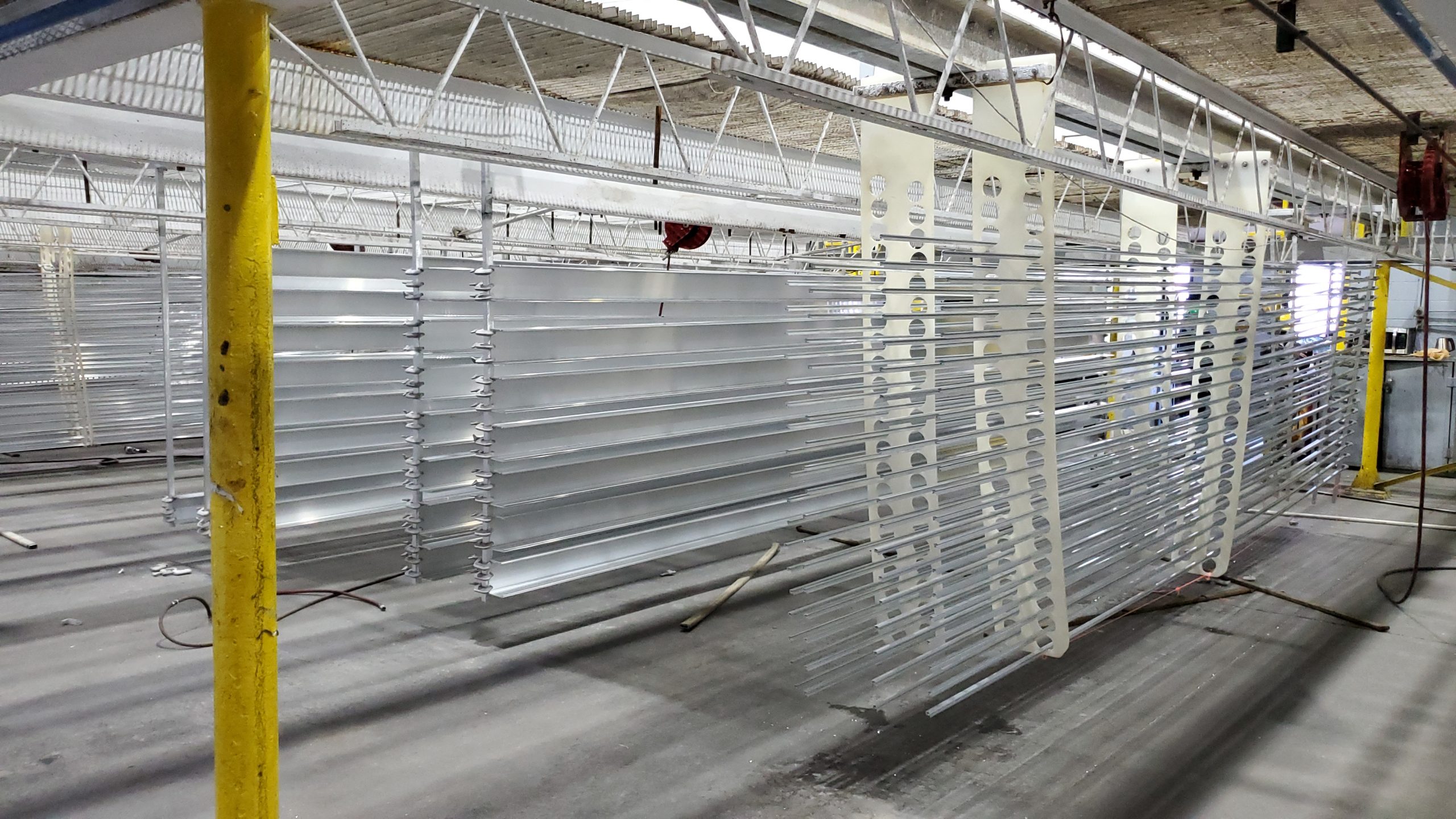
Disadvantages
- Limited color selection. Because of the chemicals used in the anodizing process, you are greatly limited on the color selection for your next project or product.
- Anodizing does not offer you the extended warranties as Superior Pigmented Painted Products.
- Touch-up of anodized product that is severely damaged in your shop or the field is more noticeable than air dry touch up paint for painted products.
Types of Anodizing
There are many different types of anodizing. Sulfuric acid anodizing is most common as it produces a porous oxide layer. There are other processes where other electrolytes are used such as chromic acid, phosphoric acid and sulfuric-boric acid. Using these different electrolytes produces oxide layers with different properties than those produced with sulfuric acid. In addition, process conditions such as temperatures can be changed to produce very hard oxide coatings.
There are three different types of Anodizing:
- Type I – anodize refers to chromic acid anodizing.
- Type II – anodize is nominal “clear” sulfuric acid anodizing.
- Type III – is “hardcoat” using sulfuric acid or mixed chemistry electrolytes.
All types are describe in detail in the anodizing standard, MIL-A-8625.
The Anodizing Process
Anodizing is a process for finishing aluminum alloys that employs electrolytic oxidation of the aluminum surface to produce a protective oxide coating.
The typical process includes cleaning, pretreating, anodizing, coloring (optional), and sealing.
- Cleaning – Generally accomplished by soaking the aluminum for several minutes in a water-based solution containing mild acids or alkalies along with dispersants and detergents to remove oils or compounds.
- Pretreatment – The most common pretreatment is etching the aluminum by which the material is dipped in a caustic soda (sodium hydroxide). The etch imparts a satin or matte finish by dissolving aluminum from the surface in a microscopically irregular pattern. After etching, the material is dipped in an acidic desmut/deoxidizer solution to remove any residue of alloying agents or oxides.
- Anodizing – This part of the process actually produces the anodic coating. It is accomplished in an electrolytic cell using sulfuric acid as the electrolyte. The aluminum is made the positive electrode and when a direct current is passed through it, water is decomposed, liberating oxygen at the surface of the metal. The oxygen combines with the aluminum to form the coating (a transparent and microscopically porous layer of aluminum oxide). The thickness of the coating is determined by the amount of electrical current and the length of time the aluminum is charged.
- Coloring (optional) – There are two possible processes – integral or two-step. Integral coloring is accomplished by imparting color to the coating as it is being formed in the anodizing bath. Two-step coloring is accomplished by imparting coloring to the porous coating after it is formed (absorbed).
- Sealing – The micro pores of the anodized coating must be sealed to prevent unwanted stains later on. Sealing is accomplished by dipping the aluminum in a hot water solution of metal salts.
Classification of anodic coatings:
- Class I – High performance anodic finishes used in exterior applications receiving periodic maintenance such as curtain walls, store fronts, and commercial windows. Minimum coating thickness of 0.7 mil (18 microns).
- Class II – Commercial anodic coatings used in interior applications or exterior applications receiving regularly scheduled cleaning and maintenance. Minimum coating thickness of 0.4 mil (10 microns).
AAMA Specifications
Keymark Corporation is 100% compliant of the following AAMA specifications: